Chemists at Rice University treated waste plastic to capture carbon dioxide from flue gas streams more effectively than current methods.
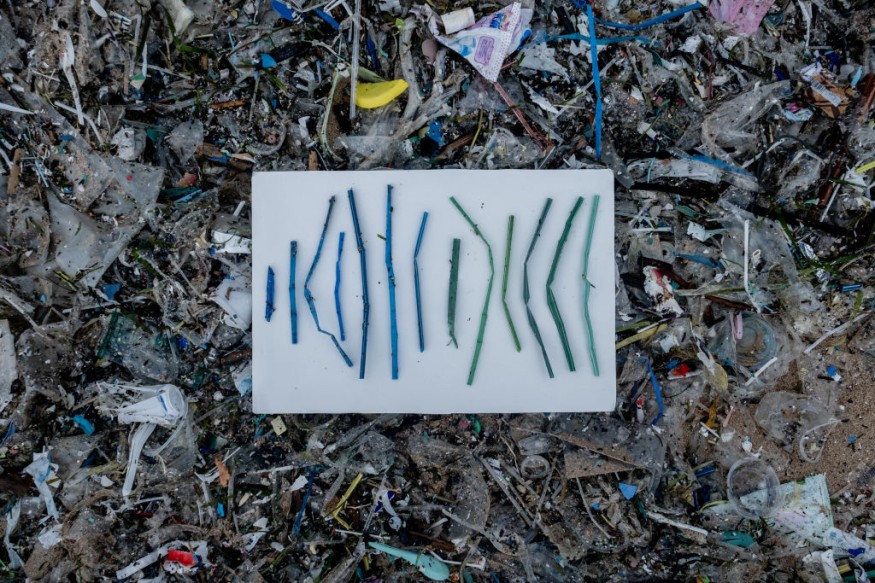
A Rice University lab's recently found chemical process for turning waste plastic into an efficient carbon dioxide (CO2) sorbent for the industry to be a win-win for a pair of critical environmental challenges.
Processing Trash
Heating plastic garbage in the presence of potassium acetate created particles with nanometer-scale holes that trap carbon dioxide molecules, according to Rice scientist James Tour and co-lead authors Rice alumna Wala Algozeeb, graduate student Paul Savas, and postdoctoral researcher Zhe Yuan.
Extracting CO2
They claimed that these particles may be utilized to extract CO2 from flue gas streams.
"Point sources of CO2 emissions, such as power plant exhaust stacks, may be equipped with this waste-plastic-derived substance to remove massive volumes of CO2 that would otherwise flood the atmosphere," Tour explained.
"It's a fantastic method to solve one issue, plastic trash, while also addressing another one, CO2 emissions."
Read also: 'Lacks Facility for Storing Toxic Waste:' Experts Comment on Expensive Nuclear Plant in the UK
Chemical Recycling
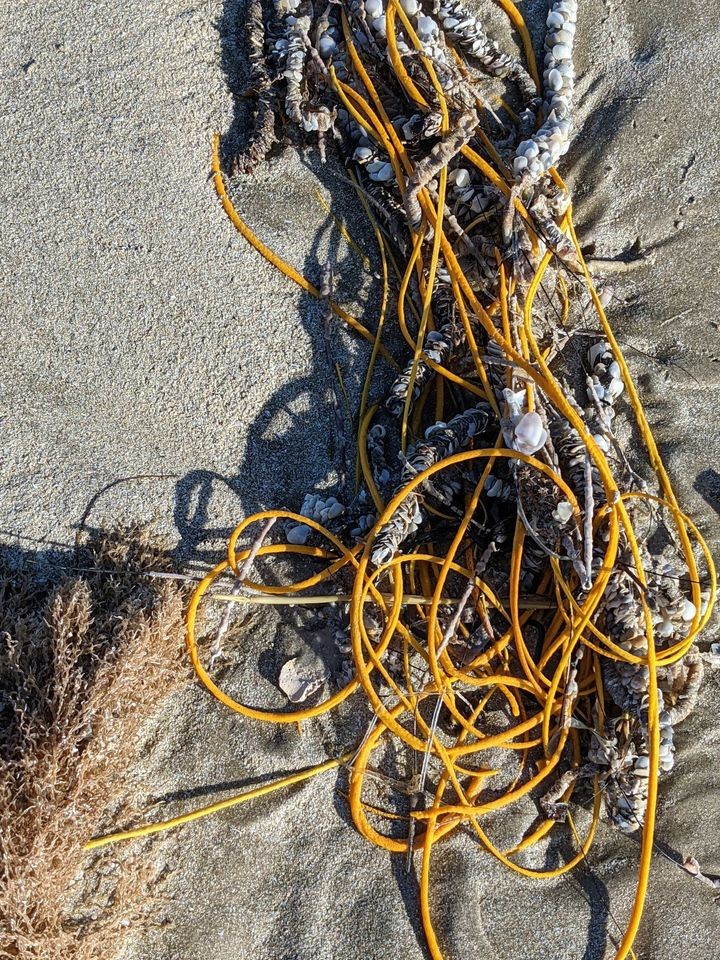
Chemical recycling, which is now used to pyrolyze plastic, yields oils, gases, and waxes, but the carbon residue is essentially worthless, according to him.
When plastic is pyrolyzed in the presence of potassium acetate, porous particles are formed that can store up to 18% of their weight in CO2 at room temperature.
Furthermore, while traditional chemical recycling does not work for polymer wastes with low fixed carbon content to generate CO2 sorbent, such as polypropylene and high- and low-density polyethylene, which are the main constituents in municipal waste, when treated with potassium acetate, those plastics work exceptionally well for capturing CO2.
Carbon Capture
The lab predicted that capturing carbon dioxide from a point source, such as post-combustion flue gas, would cost $21 per ton, significantly less than the energy-intensive, amine-based approach used to extract carbon dioxide from natural gas inputs of $80-$160 per ton.
The sorbent, like amine-based compounds, may be reused.
When heated to around 75 degrees Celsius (167 degrees Fahrenheit), trapped carbon dioxide is released from the pores, renewing roughly 90% of the material's binding sites.
Polyvinyl chloride vessels are adequate to replace the costly metal vessels generally required since they cycle at 75 degrees Celsius.
According to the researchers, the sorbent is likely to last longer than liquid amines, reducing downtime due to corrosion and sludge development.
Manufacturing
To manufacture the material, discarded plastic is ground into a powder, combined with potassium acetate, and heated for 45 minutes at 600 degrees Celsius (1,112 degrees Fahrenheit) to improve the pores, mostly 0.7 nanometers wide.
Pores widened as the temperature rose.
According to the researchers, the procedure also yields a wax residue that may be repurposed into detergents or lubricants.
Rice alumni Zhe Wang and research scientist Carter Kittrell and University of Houston graduate student Jacklyn Hall and Praveen Bollini, an associate professor of chemical and biomolecular engineering, are co-authors of the work.
Related Article : Oil, Gas, and Coal Mining Must be Regulated by 2050 to Avoid Catastrophic Global Warming
For more news about making the environment sustainable, don't forget to follow Nature World News!
© 2025 NatureWorldNews.com All rights reserved. Do not reproduce without permission.