A new approach for converting single-use plastic waste into ready-to-use molecules for jet fuels, gasoline, and lubricants has been developed by researchers - hydrocracking.

It uses only as much oil as other systems and emits no carbon dioxide into the atmosphere.
Per year, millions of tons of plastic wind up in landfills. It's a major cultural problem with far more significant environmental implications.
Plastic waste is recycled at a rate of less than 9% in the United States. Instead, more than 75% of plastic waste is disposed of in landfills, with 16% being burnt, releasing poisonous gases into the environment.
The University of Delaware's Center for Plastics Innovation (CPI) has developed a clear approach for converting single-use plastic waste, such as plastic bags, yogurt cans, plastic bottles, and bottle caps, wrapping, and more, into ready-to-use molecules for jet fuels, diesel, and lubricants.
UD Development Research
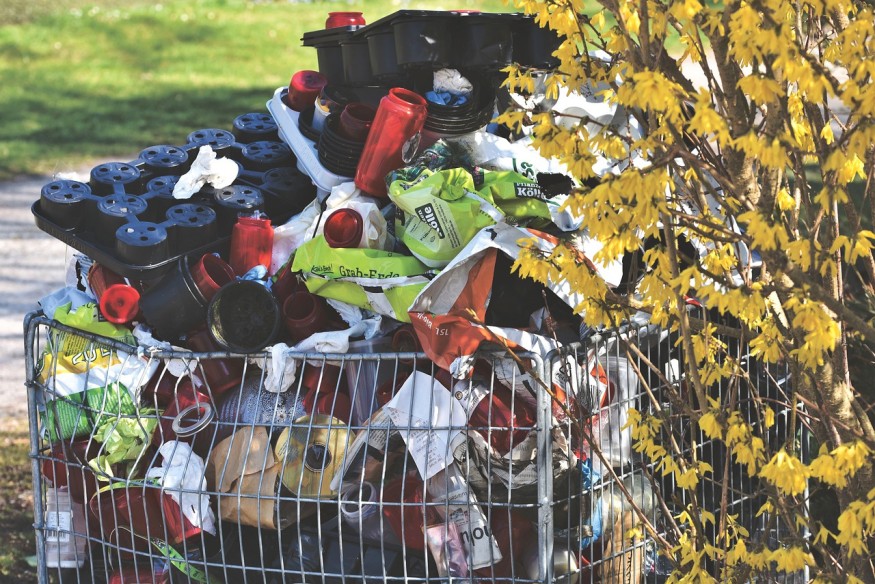
The UD-developed technology uses nearly 50% less energy than other processes. It does not emit carbon dioxide into the atmosphere, resulting in a reduction in emissions than other widely used techniques. It takes just a few hours at a low temperature of about 250 degrees Celsius. This is significantly higher than the 450°F oven temperature you would use at home to roast vegetables or bake puff pastry.
The University of Delaware researchers used a chemical method called hydrocracking to break down the plastic solids into smaller carbon molecules and inserted hydrogen molecules on both ends to stabilize the substance.
What is Hydrocracking?
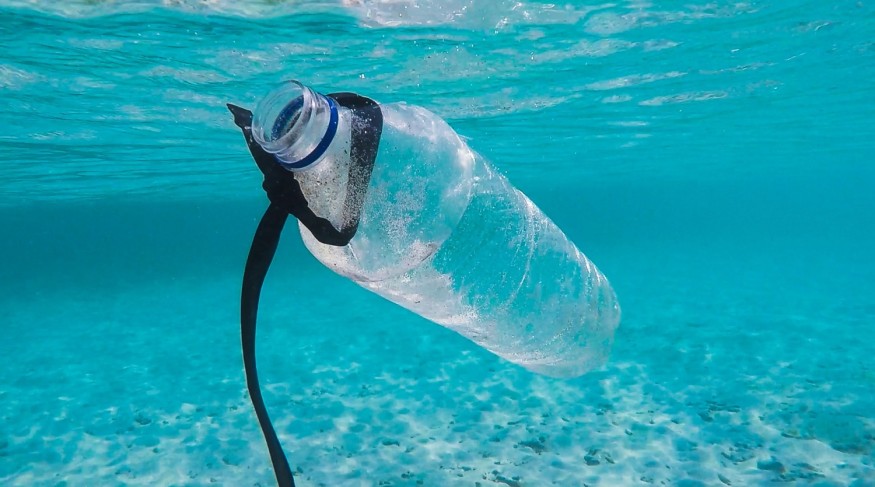
Hydrocracking is a catalytic cracking method that is aided by the addition of hydrogen gas.
Unlike a hydrotreater, it requires hydrogen to break C-C bonds (hydrotreatment is conducted before hydrocracking to protect the catalysts in a hydrocracking process). This technology was used to refine 265 106 tons of petroleum in 2010. Vacuum gas oil, a heavy fraction of gasoline, is the primary feedstock.
Catalytic Cracking

Catalytic cracking isn't a new idea. For years, refineries have used it to convert heavy crude oil to gasoline.
The system used by the study team, on the other hand, does more than just break down the plastic. It also transforms the substance into branched molecules, allowing it to be converted more precisely into a finished product.
Vlachos, who also heads the Delaware Energy Institute and the Catalysis Center for Energy Innovation at UD, said, "This makes them ready-to-use molecules for high-value lubricant or fuel applications."
Reducing plastic waste by chemically turning it into fuels can help drive a circular economy, in which goods are recycled into new products rather than being tossed out at the end of their useful lives. The recycled materials may be reused to create the same product or, in the case of oils, upcycled into higher-value goods, resulting in economic and environmental benefits.
What Comes Next?
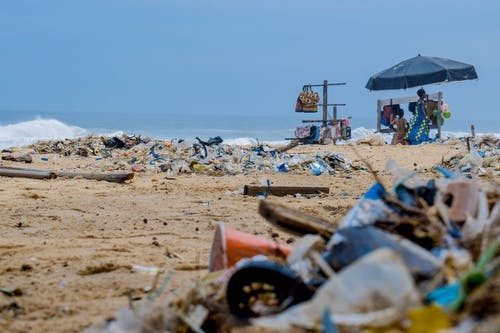
The next step in the CPI study will be to see what other plastics and materials the team's approach can handle. To start, Vlachos said the group plans to extend partnerships with colleagues around campus and in the Center for Plastics Innovation to look at other ways to create valuable materials by reducing waste.
For more environmental news, don't forget to follow Nature World News!
© 2025 NatureWorldNews.com All rights reserved. Do not reproduce without permission.