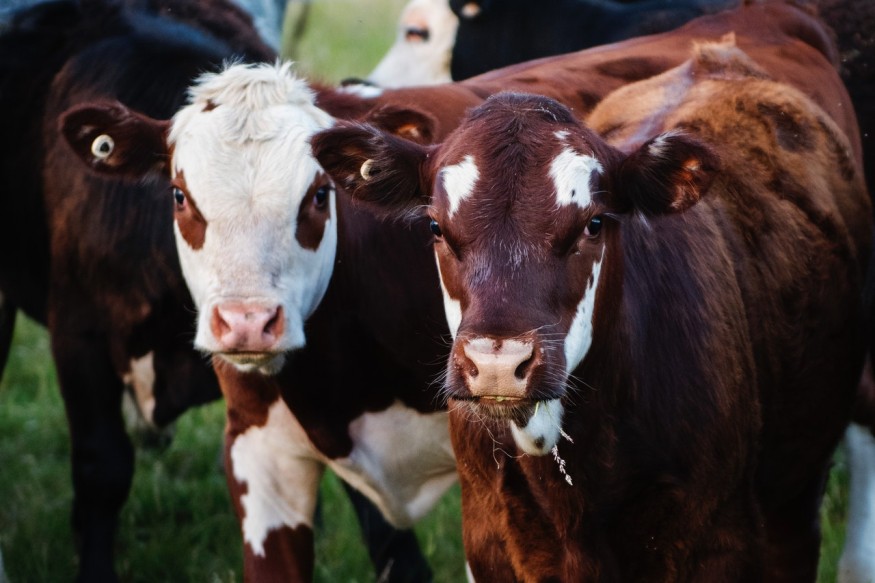
When we think of automation and the processes that are on the brink of revolutionising many key sectors, agriculture is probably not the first industry that springs to mind. Typically pictured as a demanding line of manual work that still harbours a lot of back-to-basics practices, automation has actually been around in the world of farming for decades now in the form of robotic milking.
Since the 90s, farmers have been utilising semi-automated milking processes to overhaul and optimise what was previously a hugely laborious process. However, tech developments in the last few years have seen robotic milking become a truly automated, intelligent mechanism. Here, we look at how the latest robotic milking systems are helping today's farmers navigate the ongoing challenges of the industry.
What is robotic milking?
While milking machines have been around since the early 20th century, robotic milking systems, often referred to as automated milking systems (AMS), were introduced in the early 90s and allowed farmers the option to milk their herds robotically. In the last few years, the most modern AMS have enabled the process to be carried out without any need for manpower - a far cry from traditional processes of times gone by that demanded significant labour resources and were incredibly strenuous and time consuming.
While traditional systems require herds to be corralled into milking parlours twice a day and have machines manually fitted to each cow, an AMS allows cows to approach the milking machines as they please - which is why they are also known as voluntary milking systems. Utilising smart technology, modern AMS are able to identify which cows are ready for milking, while also managing other key areas like manure removal, creating a highly efficient, time and resource saving solution.
How does it work?
How does a system allow cows to be voluntarily milked to an efficient level? The AMS utilises motivations and incentives for the cow, namely the pressure of a full udder and feeding stations in the machines, to approach the machine.
Using an electronic tagging system and smart gates, the AMS can identify and herd cows ready for milking into the machine gates. Once the cow is at the machine, an automatic brush cleans the udder before a pump is sensitively attached by a robotic arm with the aid of positioning sensors. Further sensors monitor the milk flow to ensure that no cow is over- or under-milked. Once finished, the cow is cleaned again while the milk is directed to a bulk tank to be filtered and cooled.
Regular maintenance of these machines is essential, with the typical AMS costing somewhere in the region of £120,000. All machines should be subject to regular cleaning and hygiene checks to ensure efficient and safe running.
What are the benefits?
The benefits of today's AMS are huge for farmers and the industry as a whole:
Huge time saving benefit against traditional processes - removing hours from daily workload
Huge manpower reduction against traditional processes
Milk yield is typically around 10% higher in an automated system
Herds are happier, treated better and enjoy better conditions
The growing servicing industry for AMS is developing new opportunities for dairy engineers and growing that part of the agricultural job market
Robotic milking is nothing new in farming, but the levels of automation are. With the latest AMS providing farmers with a completely labour free, optimised milking solution, farms are becoming better run, resourced and managed - setting the foundation for further automation prospects in the sector.
© 2025 NatureWorldNews.com All rights reserved. Do not reproduce without permission.